Welding Slag Inclusions: How to Prevent and Remove Them
If you are not careful with stick (SMAW) or flux-cored (FCAW) welding, you will probably get slag inclusions in the bead. After reading this article, you will know how to prevent and correct this defect.
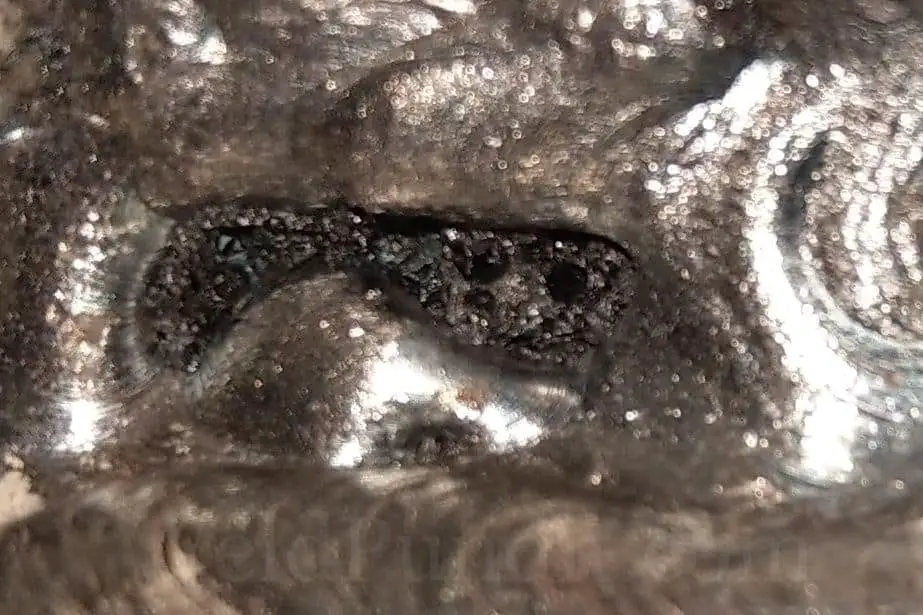
Table of Contents
- What are slag inclusions in welding?
- What are the effects of slag inclusions?
- What can cause slag inclusions in welding?
- How to prevent slag inclusions?
- How to correct slag inclusions?
- Conclusion
What are slag inclusions in welding?
Slag inclusions is a welding defect where parts of molten slag material solidify in the weld metal. These inclusions appear only with processes that use flux material, such as stick and flux-cored welding.
Slag comes from the flux material that is around a stick welding electrode (or rod) or inside a flux-cored wire. When MIG or TIG welding, you can get other nonmetallic inclusions, but not slag inclusions.
When these consumables burn, a part of their flux melts and travels through the arc into the puddle as slag droplets. Τhe slag’s job in the puddle is to clean the molten metal from various impurities and prevent oxidation.
After that, the molten slag floats to the surface by pressure differences. On the surface, it will continue to protect the hot bead from oxidation as it cools down and solidifies.
With poor welding practices described later in the article, a part of the slag material may not rise to the surface. If that happens, they solidify in the final weld as inclusions.
Shape and location
Most of the time, slag inclusions come in the form of numerous porous fragments with irregular shapes and sizes.
Sometimes inclusions can be long and narrow, running along the edges of the bead. In this form, they are also called wagon tracks.
Often, inclusions are visible on the surface of the weld. This is good because you are aware of their existence so that you can remove them.
But many times, inclusions can be hidden inside the bead. If so, they are detectable only with specialized methods.
Slag inclusions can also exist between the unfused parts of the bead and the base metal. But also between the unfused beads of multipass welds.
What are the effects of slag inclusions?
The most common slag inclusion effects are gaps in the bead and lack of fusion between the bead and the workpiece or between multiple beads.
Furthermore, the gaps may concentrate moisture and start rusting. Corrosion can also occur if the electrode’s flux had corrosive chemicals such as fluorides (7018).
Slag inclusions are porous, resulting in a weld with less metal density and strength. Any stress the weld takes will concentrate on the remaining metal.
Depending on the inclusions’ extent and the weldment’s service conditions, inclusions can lead to failure. Slag inclusions are not acceptable for critical work.
What can cause slag inclusions in welding?
There are many causes of slag inclusions. Some prohibit the correct control and flow of the molten slag. Others cool down the slag prematurely or interfere with the arc.
1. Low amperage
- If the amperage is low, the arc is not strong enough to push the slag back. The slag may run ahead of the puddle and closer to the cold unwelded metal, and it will solidify. After that, the molten metal will solidify around it, resulting in inclusions.
- Low amperage provides low heat that hinders the slag’s fluidity, so it cannot rise to the surface in time.
- Finally, low amperage makes the puddle cool down faster, increasing the risk of inclusions in general.
2. Incorrect electrode angle
- If you position the electrode perpendicular to the joint, you don’t have a proper angle to push the slag back.
- Also, the arc cannot melt the workpiece quickly enough to keep creating a crater, and the slag will cool down.
3. Bad traveling speed
- If the traveling speed is too fast, you will move the puddle on the cold metal, and it will solidify.
- Also, high speed can cause undercuts where slag can concentrate.
- With low speed, you will have high slag build up, and it will run ahead of the puddle.
4. Wrong electrode manipulation
- If you keep a long arc length, the arc spreads out and is not concentrated enough to push the slag back.
- With a weaving technique, you must be careful not to overdo it because the slag will cool down.
- If you cannot keep the electrode on the joint and wander off, you will leave gaps that fill with slag.
- Also, frequent electrode restarts increase the inclusion risk.
5. Insufficient cleaning of the joint
- If you weld on previous beads, you must remove all residual slag. Even if a small amount of slag is left behind, it is not certain that it will burn off when you weld over it.
- Also, it would help to clean all the mill scale, rust, paint, or other impurities next to the joint. The heat pulls them inside the puddle, and they increase slag inclusions or form their own. They also act as insulation against electricity and heat. This prevents the slag from wetting out and being controllable.
6. Gaps and asymmetries in the joint
- If the joint’s fit-up leaves gaps, the molten slag can concentrate there and solidify.
- Each bead of a multipass weld needs to have a flat and symmetrical surface. So there will be no big gaps between them.
- If there are undercuts from previous welds, they can fill with slag.
- Also, if the workpiece is too big and thick, it can absorb the welding heat too fast. This can cool down the slag even if the amperage and the traveling speed are correct.
7. Poor electrode selection
- You must be careful so that the electrode’s diameter is not too big for the joint’s size.
- If the electrode’s flux material is damaged in any way, for example, if it has cracks or wrong moisture levels, it can cause an arc erratic.
- Inclusions get worse if you use an unsuitable electrode for out-of-position welding.
8. Arc blow
Finally, arc blow caused by external magnetic fields can alter the arc’s path even if you move the electrode with precision.
An affected arc will create uneven metal deposition and undercuts that will fill with inclusions.
How to prevent slag inclusions?
Knowing how to prevent slag inclusions will save you a lot of time from correcting them.
1. Set the amperage high enough
It would be best to use the highest amperage for the present electrode and joint. Just a step before too much heat can cause defects.
This way, you can push the slag back and keep it fluid enough to rise to the surface.
For flux-cored, after setting the correct wire speed, make sure you set enough voltage so that the arc melts the wire and the base metal at a good rate.
2. Pull the electrode at the correct angle
First, you always pull the electrode with the stick or flux-cored processes. If you push, it is almost impossible to keep the slag at the backside of the puddle. The only exception is when welding vertical-up.
Keep the rod at a 10-20 degree traveling angle from vertical. If you use rutile rods, a bigger angle, for example, 30 degrees, is better.
If you use flux-cored, pull the torch at 5-15 degrees.
When welding out of position, you use smaller traveling angles.
3. Use the proper traveling speed
When you point the electrode at the correct angle, the proper traveling speed is when the arc points at the leading 1/3 of the puddle.
If you pull the electrode faster, the puddle will have a smaller size and stay behind.
If you pull slower, you will point the arc over the puddle and the puddle will build up too much.
4. Focus and weld with correct electrode manipulation
When stick welding, keep the arc length no longer than the rod’s wire diameter. Flux-core can autocorrect small arc length changes and makes things easier.
Use straight beads (stringers) at a maximum width of two rod-wire diameters. Try to keep the arc where it can evenly deposit the metal in the joint. Avoid frequent stops and restarts as much as possible.
5. Weld over clean metal
Clean the joint from any surface impurities such as rust, mill scale, paint, or coatings, for instance, galvanized steel. Clean the slag left from previous beads because it’s not certain that the arc will burn all of them.
After you use a chipping hammer on the slag, remove the remaining with a wire brush. Or you can use an angle grinder with a cable twist wire wheel for faster results.
6. Ensure good joint fit-up without asymmetries
A joint with a good fit-up is symmetrical without gaps where the slag can concentrate and solidify.
Differences in metal thickness, either at the root face or total thickness, can also cause problems.
If there are undercuts from previous passes, correct them with an angle grinder. Do the same if previous beads are too convex or have any other asymmetries.
Also, if the workpiece is very thick, preheat the joint.
7. Select the proper stick rod or flux-cored wire size and type
When stick welding, select the correct rod diameter, so it can properly fit in the joint.
The rod’s flux must be in good condition. Protect rods with a basic flux such as E7018 from excess moisture. But you want to prevent rods with a cellulosic flux such as E6011 from losing their moisture.
Keep in mind that electrodes with a rutile flux such as the E6013 rods tend to create more inclusions.
Also, for out-of-position welding, pick an EXX1X rod or an EX1T wire. 1 means they can weld at all positions.
But if you weld vertical down, you want to choose true all-position rods, such as the E6010 or the E6011. These can freeze very fast without the slag running ahead, causing inclusions.
8. Check for and avoid external magnetic fields
If you weld with DC, you must check if there are external magnetic fields close to the arc. For example, if you weld close to welding magnets, or you weld on a magnetized welding table.
If you weld with AC, arc blow is seldom an issue. You can read this WeldPundit arc blow article to learn more about it.
How to correct slag inclusions?
The proper way to correct slag inclusions is to remove the affected part of the bead, then weld it again.
Many welders try to correct slag inclusions by burning them with additional passes, especially when using cellulosic rods such as the E6011.
These rods have a very aggressive arc that digs deep into the metal and can burn residual inclusions. The final bead may look good without any visible inclusions.
But if you weld like this, you can never be sure that there are no inclusions left inside the final weld.
Remove inclusions with an angle grinder
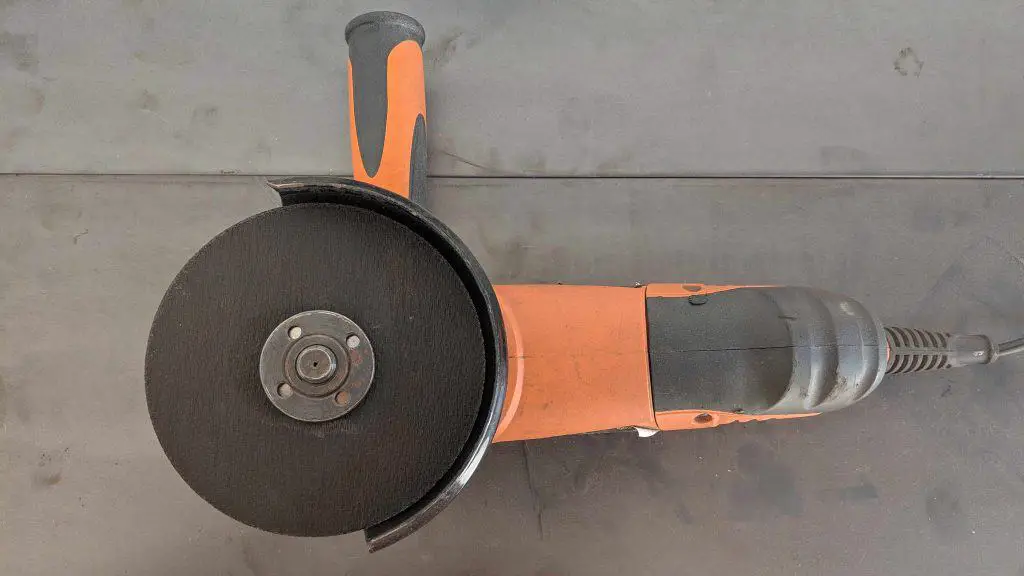
Removing slag inclusions with an angle grinder is simple, cheap, and effective.
To remove the affected weld metal, use the angle grinder perpendicular to it. Cut-off wheels are ideal for this since they are made to work with their edges.
But which cut-off wheel? Thin wheels, for example, .040″ (1 mm) cannot remove a lot of material, and more importantly, they are prone to shattering. Wheel shattering is one of the most dangerous things to happen when using a grinder.
The 1/8″ (3.2 mm) cut-off wheels are the best choice since they are thick enough and safe, offering fast material removal.
When removing weld metal with a wheel, the best technique is to pull the grinder. Back and forth movements are not the best for this kind of work. You can tilt the grinder a bit to help remove more metal.
Make sure when you select a wheel to be suitable for each metal you work with. Also, check that the maximum rotations per minute mentioned on the wheel are at least as many as those mentioned on the angle grinder.
Grinding wheels are not suitable to remove inclusions because their edge can work only at a 5-15 degree angle and not perpendicular. If you use them perpendicularly, you will damage them.
Ordinary flap discs are also not suitable for the same reason. There are flap discs with curved edges for perpendicular work, but they are hard to find.
Gouging processes to remove inclusions
While an angle grinder is good enough for most cases, I will mention some heavy-duty gouging processes to remove inclusions.
- Arc gouging is the simplest one. It uses a stick power supply and does not need compressed air. The only difference is the special gouging rods.
- Oxyfuel gouging is popular and uses oxyfuel cutting equipment, but only works with a few metals, such as carbon steel.
- Air carbon arc gouging is considered a “violent” process and uses a high-amperage stick power supply, a gouging torch, special rods, and compressed air. It is very efficient but doesn’t offer pretty results, especially for stainless steel.
- Plasma gouging is the best one, but also the most expensive. It uses plasma-cutting equipment.
Conclusion
Slag inclusions are a common defect with the stick and flux-cored processes. If they are excessive, they make the joint weak and prone to failure. They can also start corrosion.
Low amperage, wrong electrode angle, and slag material from preceding welding are the main reasons for slag inclusions.
More WeldPundit articles