Vertical Stick Welding: Settings, Techniques, and Charts
When you try to stick weld vertically, either up or down, you will see that it’s much harder than the flat position. The weld metal and the slag drip down uncontrollably, along with increased sparks and spatter.
In this article, you’ll learn the basics of vertical stick welding (SMAW) to help you get satisfactory results faster.
To keep things simple, we’ll focus on vertical fillet (3F) and groove (3G) welds and the most popular rods for mild steel.
The proper term when you weld upwards is vertical-up welding, but we also call it uphill. When you weld downwards, it’s vertical-down or downhill.
Table of Contents
- Can you stick weld vertically?
- Should you stick weld up or down?
- Is it easier to stick weld up or down?
- What polarity to use?
- Vertical stick welding amperage per metal thickness in inches and mm
- Arc force (dig) for vertical welding
- Arc length for vertical
- What is the best rod for vertical welding?
- Vertical welding with 7018
- Vertical welding with 6011 and 6010
- Vertical welding with 6013
- Tips for vertical stick welding
- Conclusion
Can you stick weld vertically?
First, let’s see how capable stick welding is to weld vertically.
You can stick weld vertically, depending on the welding rod you use. The nature of the rod’s flux covering indicates how suitable it is to weld up or down, or not at all. If the rod’s designation’s second from the last digit is 1 (Exx1x), you can weld vertically. If it’s 2 (Exx2x), you cannot.
You can stick weld uphill with all Exx1x rods, but not all of them are good downhill:
- The basic or low-hydrogen rods such as the 7018 cannot weld downhill.
- The rutile rods such as 6013 can weld downhill if you select diameters 1/8″ (3.2 mm) or thinner.
- Only the cellulosic 6010 and the 6011 are true downhill rods and offer excellent welds without defects.
Furthermore, the thickest rod for vertical welding is 5/32″ (4 mm) for basic rods and 3/16″ (4.8 mm) for cellulosic rods. After that, the puddle is too large to control.
One well-known rod that cannot weld vertically is the rutile 7024 because it has a large amount of iron powder in the flux covering (50%). The excessive iron creates a large and very fluid puddle that cannot stay in place.
There is also the Exx4x designation. Rods with this flux covering, such as the E7048 were designed for downhill pipe welding. However, these rods are not available on the market.
Should you stick weld up or down?
For thick metals, you weld uphill because you can penetrate the joint deeper and get stronger joints. Furthermore, you have improved puddle control and visibility. Downhill is suitable for open root pipes and thin metals.
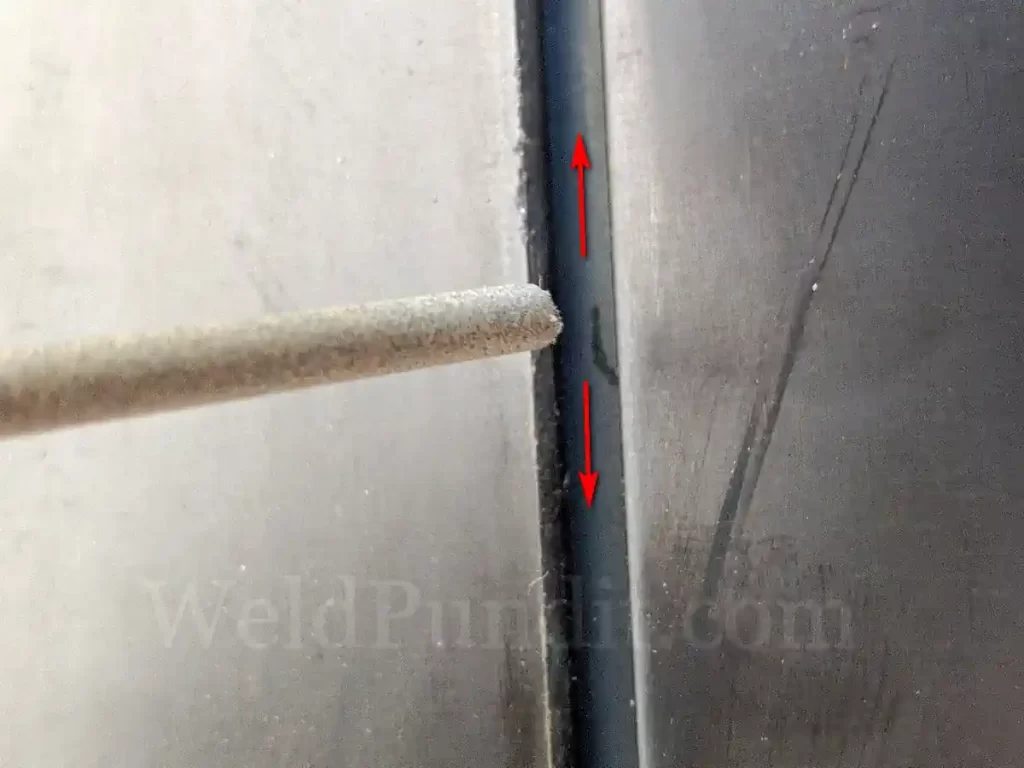
- Uphill is necessary if your metal is 1/4″ (6.4 mm) or thicker.
- If the metal is between 1/4″ and 1/8″ (3.2 mm), you can weld it uphill if it’s a fillet weld. Weld it downhill if it has an open root.
- If it’s 1/8 or thinner, weld it downhill to prevent warping or even blowing through the metals.
Uphill stick welding
When you weld with a stick rod, you always pull the rod to keep the slag material back. The only exception to this rule is uphill welding. Now gravity keeps the slag down, and you can push the rod.
This way, the arc points to the metals and melts them faster for deeper penetration. For the same reason, you have better puddle visibility.
For uphill, you want a smaller puddle and a slower traveling speed than the flat position to control it easier. You create a small puddle by selecting a thinner rod, setting a lower amperage, and keeping a tight arc length.
As a general rule, the correct traveling speed for both up and down welding always points the arc on the first 1/3 of the puddle.
The slow speed combined with the strong arc of stick welding can burn off coatings such as galvanization, mill scale, rust, or their residues. The trade-off is that you cannot stick weld thin metals uphill.
The uphill traveling angle for all rods is 5-10° below horizontal.
Bead types for uphill
Uphill allows you to manipulate the puddle in various ways and create different beads to fill the joint.
Stringers (straight beads) are often used for the first pass. They can fuse the metals with a low heat input, creating stronger joints.
However, vertical stringers have irregular and convex surfaces and need many passes to fill a thick joint. This can result in lack of fusion problems between each pass.
After the first pass, you can use weave beads to create a shelf that supports the puddle as you weld. They are practical and quite popular for uphill welding.
Wide weave beads are slow but deposit a lot of weld metal in the joint. As a result, you only do a few passes, even for thick metals. They also create a symmetrical bead with a flat surface.
Weave beads are suitable for 1/4″ or thicker metals. If you want to weld uphill thinner metals, use stringers to prevent overheating.
The most popular is the “Z” weave, a tight variation of the “W” (zigzag) weave:
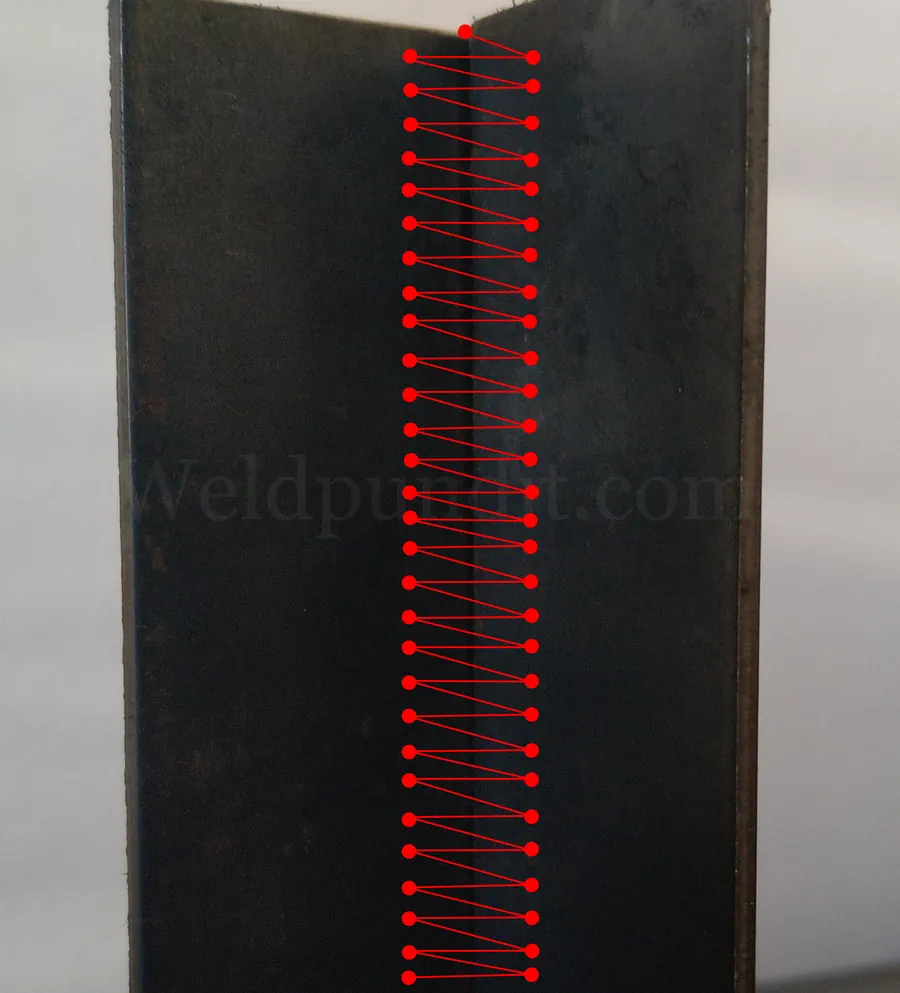
- You create the puddle over the edge (toe) of the previous bead.
- Move the rod to the other toe in a straight line and pause for one second.
- Then move the rod to the starting side in a diagonal line with a tight angle and pause again.
- Repeat steps 2 and 3 until you finish. You move fast between the toes to avoid a convex bead. The metal will flow on its own to cover the center.
When the rod points at one side, the other one freezes and creates a shelf that will support the following puddle as you progress upwards.
The brief pause at each side melts the base metal to avoid lack of fusion and fills it with weld metal to avoid undercut. An undercut is when the sides melt but don’t fill with weld metal. The pause will also burn any leftover slag material.
The maximum “Z” weave width is six times the rod diameter to prevent high-temperature differences between the two sides.
Uphill and arc blow
Because uphill is very slow, the top section of the metals can get red-hot as you weld. That may result in a defect called arc blow where magnetic forces point the arc away from the desired path.
One way to prevent these defects is to use a run-off tab, a small piece of metal (e.g., 2″x2″ x the metal thickness) with the same shape as the workpiece, tack welded at the ending of the joint.
When you reach the joint’s end, you continue on the run-off tab. The tab will absorb the excessive heat, the ending crater, and the arc blow defect. After you finish, you cut off the tab.
Downhill stick welding
When you weld downhill, there is no shelf to control the puddle. To control it, you weld straight beads at a fast traveling speed. This keeps the molten metal and the slag behind the arc.
The fast traveling speed inputs less heat into the metals, offering shallow penetration. This is ideal for preventing warping and blowing through thin metals. Another advantage of downhill is better-looking beads.
The danger of downhill is that if the puddle overruns the arc, it will act as a barrier, and the base metal will not melt. As a result, the filler metal will not mix and fuse with the base metal. We call this lack of fusion and in severe cases, it can affect the entire bead. That’s a dangerous defect because the joint can fail with the lowest load.
You can also get lack of fusion if your traveling speed is too fast. Now the arc cannot provide enough heat to melt the metal.
Furthermore, if the molten slag runs ahead of the bead, the arc will push it inside. Then it will solidify in the bead, creating slag inclusions. Inclusions will make the bead weaker and act as corrosion points. They also make the bead look horrible.
Finally, open root joints for downhill need a symmetrical fit-up and the correct gap size for the rod you want to use. That’s because you cannot manipulate the puddle to fix a poor fit-up.
The professional use of downhill stick welding is for open root joints of heavy-duty pipes with 6010 rods.
Is it easier to stick weld up or down?
Stick welding is a hard process to use, and if possible, it’s best to pick the easiest vertical direction.
It’s easier to stick weld downhill than uphill because it requires less skill to control the puddle. Downhill doesn’t need complex techniques to keep the puddle in the desired place.
The problem with downhill is that slag may overrun the puddle and solidify in the bead.
What polarity to use?
Most stick rods can burn using different polarities:
- For uphill, you set the direct current electrode positive (DCEP, or DC+) polarity because it offers the deepest penetration.
- If you want to weld downhill thin sheet metal, for instance, 14 ga (2 mm) or thinner, you can set the direct current electrode negative (DCEN, or DC-) polarity. DC- releases less heat, preventing burning through and warping. It’s also suitable for downhill open-root joints.
- If you experience the arc blow defect, using alternating current (AC) is another way to reduce the negative effects. However, use AC only if necessary because it creates a less stable arc.
Here is a table with the stick rod polarities.
Rod | Flux material | Current Type |
---|---|---|
E6010 | Cellulose-Sodium | DC+ |
E6011 | Cellulose-Potassium | AC & DC+ |
E6012 | Rutile-Sodium | AC & DC- |
E6013 | Rutile-Potassium | AC & DC± |
E7014 | Rutile-Iron powder | AC & DC± |
E7016 | Low Hydrogen-Potassium | AC & DC+ |
E7018 | Low Hydrogen-Iron powder | AC & DC+ |
E7024 | Rutile-High iron powder | AC & DC± |
E7028 | Low Hydrogen-High iron powder | AC & DC+ |
Vertical stick welding amperage per metal thickness in inches and mm
All rod manufacturers recommend an amperage range for each rod they produce. This range may vary considerably between each manufacturer.
Also, each welding machine burns the same rod differently, even if they display the same amperage. Therefore, after practicing with the following settings, it’s best to write your own chart for your equipment and preferred welding techniques.
The joint design for vertical is similar to the flat position, but try to make joints with perfect fit-up to make welding easier. If the metals are 3/16″ (4.8″ mm) or thicker, always make single-V grooves. One difference to notice is that downhill open-root joints need a 50% wider root gap and a thinner root face.
The following suggested settings are for fillet welds of tee joints with DC+ polarity but:
- For butt joints with an open root, reduce the amperage by at least 10%.
- If you weld with AC, increase the amperage by 10%.
- If your workpiece has a coating, for instance, mill scale, increase the amperage by 5%.
Depending on what you see and hear, you can set a higher or lower amperage with a step of 5A. The amperage must be high enough to prevent sticking the rod while keeping a tight arc.
The following table shows the suggested uphill amperage for each rod per metal thickness in gauge, inches, and millimeters.
As a general rule, you select a thinner rod than the flat position and set a 10-15% lower amperage to create a smaller puddle.
If you want to use 7014s instead of 6013s, they need a 10-15% higher amperage.
Rod | Metal thickness | Rod size | Vertical-up amps |
---|---|---|---|
E6011 | 11 ga / .125″ (3.2 mm) | 3/32″ (2.4 mm) | 55 |
E6011 | 7 ga / .188″ (4.8 mm) | 3/32″ | 65 |
E6011 | .250″ (6.4 mm) | 1/8″ (3.2 mm) | 80 |
E6011 | .312″ (8.0 mm) | 1/8″ | 90 |
E6011 | .375″ (9.5 mm) | 5/32″ (4 mm) | 100 |
E6013 | 11 ga / .125″ (3.2 mm) | 3/32″ (2.4 mm) | 55 |
E6013 | 7 ga / .188″ (4.8 mm) | 3/32″ | 65 |
E6013 | .250″ (6.4 mm) | 3/32″ | 70 |
E7018 | .188 (4.8 mm) | 3/32″ (2.4 mm) | 70 |
E7018 | .250″ (6.4 mm) | 3/32″ | 85 |
E7018 | .312″ (8.0 mm) | 1/8″ (3.2 mm) | 95 |
E7018 | .375″ (9.5 mm) | 1/8″ | 100 |
E7018 | .500 (12.7 mm) | 1/8″ | 110 |
The following table shows the suggested downhill amperage. As a general rule, you select the same or an even thicker rod diameter than the flat position. Then you set a 10-15% higher amperage and travel fast.
Rod | Metal thickness | Rod size | Vertical-down amps |
---|---|---|---|
E6011 | 14 ga / .080″ (2.0 mm) | 3/32″ (2.4 mm) | 55 |
E6011 | 13 ga / .093″ (2.4 mm) | 3/32″ | 65 |
E6011 | 11 ga / .125″ (3.2 mm) | 1/8″ (3.2 mm) | 100 |
E6011 | 7 ga / .188″ (4.8 mm) | 1/8″ | 115 |
E6011 | .250″ (6.4 mm) | 5/32″ (4 mm) | 130 |
E6013 | 14 ga / .080″ (2.0 mm) | 3/32″ (2.4 mm) | 65 |
E6013 | 13 ga / .093″ (2.4 mm) | 3/32″ | 75 |
E6013 | 11 ga / .125″ (3.2 mm) | 1/8″ (3.2 mm) | 115 |
E6013 | 7 ga / .188″ (4.8 mm) | 1/8″ | 125 |
You can also read this Weldpundit article on stick rod type and size selection.
Arc force (dig) for vertical welding
Many modern machines allow you to set the arc force (or dig) function. This function senses the arc length, and if you push the rod in the puddle, it increases the amperage. This way, you avoid sticking the rod.
For vertical, it’s best to set the arc force to 60% for cellulosic rods and 30% for basic and rutile rods.
If your welder has arc force, it also has the hot start function. This one increases the amperage when you strike the arc.
Weldpundit has a detailed article on hot start, arc force, and anti stick.
Arc length for vertical
One of the most common and severe mistakes when stick welding vertically, is not keeping a short and steady arc length. The arc length must be no more than one-rod diameter. That is the wire diameter without the flux covering.
Many new welders tend to keep a longer arc length to avoid sticking the rod, but that’s wrong. It’s the low amperage settings that stick the rod.
In the flat position, the side effects are not too obvious, but in the vertical, it’s the main reason for unacceptable welds.
Stick welding is hard because the rod gets shorter as it melts. You constantly push it to keep the arc length steady. This will keep the arc stable and the puddle small and easy to control.
Now let’s see how the most well-known rods perform for vertical, as well as a basic how-to for each one.
What is the best rod for vertical welding?
For vertical-up welding, the best rod is the E7018 because it deposits the strongest and most ductile weld metal. An E7018 can also fill the join faster than the other rods. For vertical-down, the best rod is the E6010 (and the E6011) because it deposits fast-freeze weld metal.
Choosing the right rod is essential for achieving satisfactory results in the vertical position. However, each rod is designed for certain jobs and requires specific angles, weave patterns, and so on.
Vertical welding with 7018
When you weld uphill, you weld thick metals with deep and wide joints, and it’s best to use 7018 rods. They have a flux covering that deposits weld metal that’s in almost every way stronger than the other rods.
Furthermore, the flux of 7018 rods contains iron powder (25%). That increases the deposition rate and fills the joint faster.
However, these rods are not suitable for downhill. Their flux generates a large amount of slag material that rolls in front of the puddle. Also, their low gas coverage doesn’t allow fast traveling speeds without porosity.
The 7018 rods need the shortest and steadiest arc length to prevent porosity problems and hydrogen from entering the joint, causing cracking issues. But that’s not a concern when working with mild steel under 3/4″ (19 mm).
Furthermore, they have a low tolerance for mill scale, rust, etc., and require a clean metal to weld.
When you weld uphill with a 7018, some slag material will drip down the weld, which is normal. If you keep a short arc length, a slow and steady speed, etc., the weld metal will stay in place, and the bead will look great.
Now let’s see the basics of how to weld uphill with a 7018 rod.
Uphill fillet welds
For a single-pass fillet weld, pass a stringer bead with or without a small side-to-side motion. Stringers will give you good penetration into the root.
You can also use the upside-down “V” pattern that keeps the arc in front of the puddle for deep penetration. The side-to-side motion is narrow, one-rod diameter. You pause briefly (less than a second) at the sides and the center. A “V” deposits more metal and leaves a flatter bead.
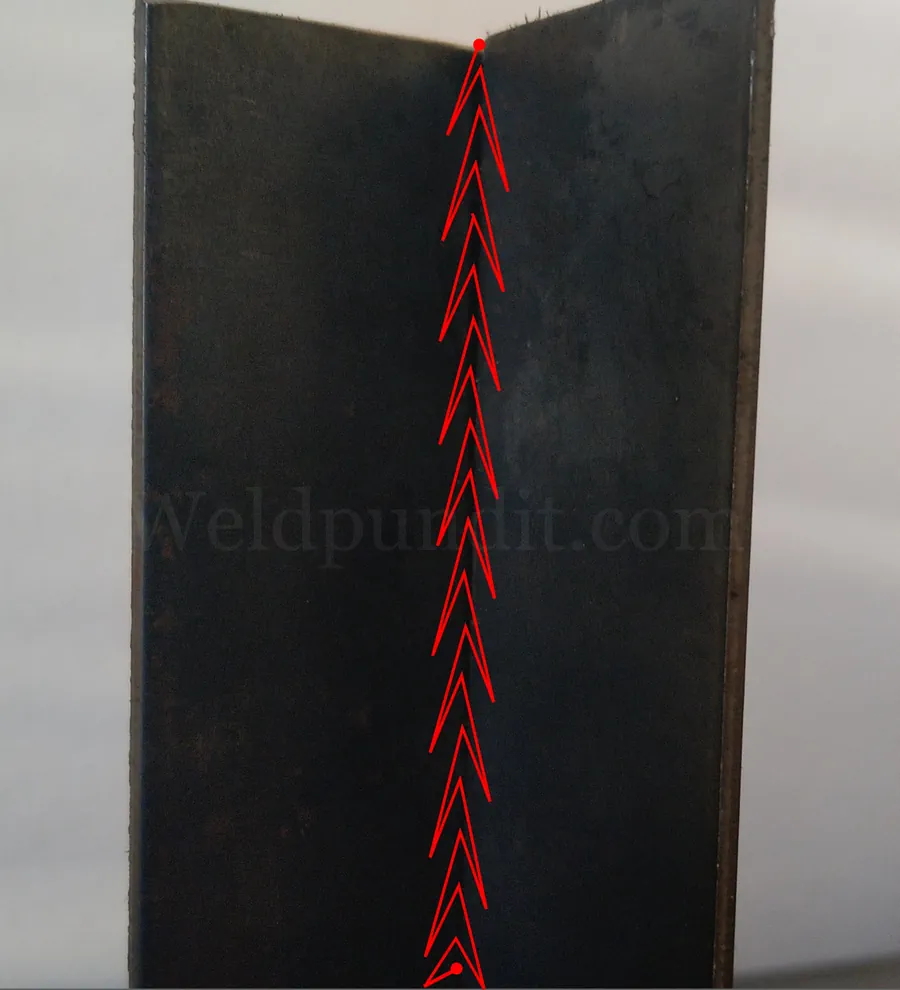
For a thicker multi-pass fillet weld:
- Weld the root pass with an upside-down “V”.
- Between each pass, clean the slag with a chipping hammer and a wire brush or a knotted wire wheel.
- For the next passes, a “Z” weave is excellent to build the shelf and fill the joint quickly. Always with a short one-second pause on the edges.
Uphill open-root welds
The 7018 rods are rarely used for an uphill open-root weld because they don’t penetrate that deep, and their puddle doesn’t freeze fast enough. However, for simple jobs, you can weld open roots with a stringer bead after considering the following:
- An unorthodox technique is to use DC- polarity. While 7018s are not intended for this polarity, they will burn beneficially for open-root welds. The puddle will be less fluid and the final weld will be more uniform.
- Leave a wider root gap than usual because 7018s have a thicker flux covering that prevents root access.
- Make sure that the groove is symmetrical because 7018 rods cannot burn through irregularities as cellulosic rods can.
- Finally, you can use an even lower amperage close to the rod’s limit to make the puddle less fluid.
The process is very slow, and the speed must be perfectly steady.
For thicker multi-pass welds, after passing the root weld, remove the slag and continue with “Z” weaves to fill the joint.
A similar rod to the 7018 is the 7016. It’s almost the same, but without iron powder in the flux. This makes the puddle freeze faster, making it better for open-root vertical welds. But this rod is hard to find, and more expensive.
For the first pass of multi-pass welds, especially for open roots, it’s recommended to use a cellulosic rod to get the best puddle control and root penetration. After that, you can fill the joint with 7018 rods.
Vertical welding with 6011 and 6010
The 6011 and the 6010 rods are great for uphill welding and are the only rods that give excellent results downhill.
However, 6010 rods have a compatibility problem. Most small welding machines cannot burn them.
The 6011 rods can work with any welding machine that also burns 7018s. You can also use 6011s with AC machines.
6011s and 6010s give similar results for regular welding. However, 6010 rods are required for heavy-duty work such as open roots of pressurized pipe.
Uphill with 6011
6011s have a flux covering that contains cellulosic material (fibers). Cellulose creates a strong arc, a lot of shielding gases, and a low amount of slag.
The strong arc can burn through rust, mill scale, or even galvanized steel. That’s important if you cannot clean your joint.
The strong gas coverage allows wide rod manipulation or even whipping the rod without losing shielding protection. This allows you to control how much heat goes into the puddle:
- For thicker metals, you whip a short distance (or not at all) to penetrate deeper.
- For thinner metals, whip further to avoid burning through or warping.
The thin slag material makes the puddle freeze fast, preventing it from dripping off the shelf.
6011 rods don’t have iron powder and are slow to fill large joints. But because they can freeze fast, you can use a thicker rod to fill the joint faster if the metal’s thickness permits it.
Uphill fillet welds
For a single-pass fillet weld with a 6011, you can weld a straight bead with the whip and pause motion:
- After you start the arc and form the puddle, you whip the rod upwards one-rod diameter to cool the puddle.
- Quickly return halfway back to add filler metal in the puddle and repeat.
You can also use the upside-down “T” weave that deposits more weld metal without leaving undercut.
- After starting the arc, move the rod to the left one-rod diameter and pause briefly. Then move two-rod diameters right and pause briefly.
- Bring the rod back to the center.
- Briefly lift it up one-rod diameter to cool the puddle.
- After that, lower the rod halfway back and repeat the cycle.
For a thicker multi-pass weld, you can use several weaving techniques:
- Weld the root pass with an upside-down “T”.
- Clean the slag.
- Because the first bead probably has a convex surface, for the next pass you can use the box weave. It’s like a “Z” weave, but when you are at the sides, you whip the rod upwards for a one-rod diameter. Then, bring it back halfway, make a brief pause, and travel to the other side. A box weave makes the second bead more symmetrical.
- For additional passes, “Z” weaves with a one-second pause on the edges are good enough to fill the joint.
This YouTube video is old, but it shows all three techniques.
Uphill open-root welds
For a single-pass open-root weld with a 6011, use a stringer bead, with or without a whipping movement, to create a small keyhole. A keyhole is a controlled burn-through at the leading edge of the puddle and offers complete root penetration.
If the joint is too tight, don’t use whipping, simply drag the rod on the root at the proper speed to control the keyhole. But if there is a wider gap, a whip and pause movement will keep the keyhole at the correct size.
For thicker multi-pass welds, after the root pass, you can continue with the box and Z weaves to fill the joint.
Downhill with 6011
Downhill with 6011 rods is simpler. You don’t use weave beads, only stringers with or without a tight puddle manipulation.
The strong arc of 6011s pushes back the weld metal and the slag, preventing lack of fusion and slag inclusions.
Furthermore, the strong gas coverage prevents porosity when going downhill at fast traveling speeds.
The traveling angle for cellulosic rods is 20° or more, depending on the application.
Downhill fillet welds
For a single-pass fillet weld with a 6011, pass a stringer without puddle manipulation. The traveling speed must be fast enough to keep the puddle back.
For a thicker multi-pass weld, pass a stringer without manipulation. Then you can choose a bigger rod and weld stringers with tight side-to-side manipulation to fill the joint.
Downhill open-root welds
For a single-pass open-root weld, drag the rod on the root at a fast traveling speed to avoid burning through the root. You don’t use puddle manipulation (whip) except if you must cool the puddle briefly to prevent blowing through.
For a thicker multi-pass weld, after the root pass, continue with another stringer and a tight side-to-side manipulation. Finally, you can use thicker rods and a wider manipulation for the following passes.
For multi-pass downhill welds, after the root pass, you can switch to uphill welding to fill the joint with fewer passes and better puddle control.
Vertical welding with 6013
The 6013 rods are the easiest rods to use and easy to find. Furthermore, even the most affordable welding machines can burn them with DC± or AC. They can weld vertically but they have limitations.
Uphill 6013
The flux of a 6013 rod creates slag that hides the puddle. This prevents you from perfectly controlling the puddle when welding uphill.
Furthermore, the weld metal is not as ductile and doesn’t have high impact resistance in cold environments as the previous rods. That’s not ideal for thick metals.
Finally, 6013 rods have low amounts of iron powder and cannot deposit a lot of weld metal. As a result, you need a longer time to fill large joints.
As an alternative, you can use 7014 rods, which are like an enhanced version of the 6013s. Their flux has iron powder (25%) to fill the joint faster. They create a stronger arc and offer better puddle visibility. But they aren’t as easy to find.
For uphill, you follow the 7018 methods, but the 6013 slag is more fluid, and it’s a bit harder to keep the puddle in place.
However, 6013s can forgive mistakes such as not keeping the arc length perfectly stable or frequently stopping and restarting the arc.
Downhill 6013
You can use 6013 rods with 1/8″ wire diameter or thinner to weld downhill. But the chances of slag inclusions are pretty high because the slag is very fluid and runs in front of the puddle.
Use a straight bead with a minimal side-to-side motion to regulate the speed and flatten the bead. Also, it’s helpful to use a large traveling angle, 30° or more, to keep back the slag.
The 6013 is the best rod to stick weld thin metals, especially if you weld them downhill with DC- polarity.
Finally, let’s see some welding tips.
Tips for vertical stick welding
When you weld uphill, you want the strongest joint. For this, it’s always best to weld on clean metal, especially for 7018 rods. Downhill welding also requires clean metals because the fast traveling speed cannot burn coatings.
Before starting, position the work in relation to your body as comfortably as possible. Your hand should not be above your chest when you finish a weld. This will give you improved stability and arc visibility.
You want to be as steady as possible to manipulate the puddle with precision. You can use your free hand to grab a nearby surface. Or make your own support using a vise-grip or tack weld a piece of metal nearby. Also, keep your working elbow close to your body.
Choose a small diameter rod 3/32″ (2.4 mm) for practice. Thicker rods create a larger puddle that’s harder to control.
To protect yourself from spatter, wear long leather sleeves or a robust welding jacket, and cover your head. Also, remove valuable equipment or cover it with welding blankets. Finally, ensure there are no flammable materials around to prevent a fire.
Another tip to make things easier is fitting the rod in the stinger pointing upwards. This way, you can keep your hand in a more comfortable position.
Before starting the arc, run a few dry runs to test your position.
Always strike the arc 1/2″ further than the point you want to start. Then bring the rod to the starting point or the previous crater. This way, you weld over the striking area and avoid asymmetries where the beads connect.
Keep an eye behind the puddle. A sagging puddle has a pointed trailing edge. To correct this, ensure you keep a tight arc and that the traveling speed isn’t too slow. You can also lower the amperage.
If you see undercut, you can pause longer at the edges, travel slower, or lower the amperage.
If you weld multiple beads uphill and the metals overheat, you can pause shortly to cool them down.
Conclusion
Vertical stick welding is hard to learn, especially going upwards.
Uphill welding is necessary for thick metals because it penetrates deeper, uses weaving for better puddle control, and minimizes slag inclusions.
The best way to weld a thick joint uphill is by using a 6010 or 6011 rod for the root pass and 7018 rods for the next passes.
Downhill stick welding is great for pipe open-root welds and metals too thin to weld them uphill. The best rods for downhill are the 6010 and the 6011 or a 6013 for thin single-pass joints.
Vertical-up | Vertical-down | |
---|---|---|
Recommended welding rod | E7018 | E6011 |
Rod size | One-size thinner than flat | Same or one size thicker |
Amperage | -15% | +15% |
Beads | Stringers, weaves | Stringers |
Traveling angle | 5-10° | 20°+ |
Traveling speed | Very slow | Fast |
Metal deposition | High | Low |
Bead shape | Convex | Concave |
Common Problems | Fluid puddle, undercut | Lack of fusion, slag inclusions |
Weldpundit articles
How to Stick Weld Stainless to Carbon Steel: Step by Step.
Is Stick Welding Easy or Hard to Learn? And How Long It Takes.