How to Stick Weld Galvanized Steel in 7 Steps
Stick welding is the best process to weld galvanized steel, but galvanization makes welding difficult. While it’s best to remove the coating, sometimes you don’t have the equipment to do so, or you want to skip this step to save time.
Because I’ve stick welded a considerable amount of galvanized steel, I decided to write this guide so new welders can avoid the problems caused by the coating.
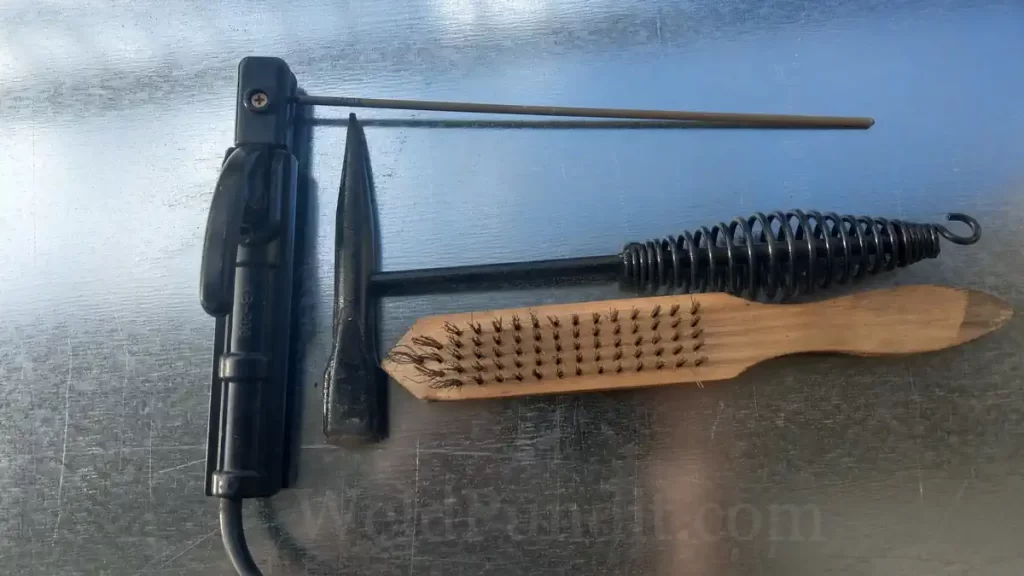
First, a few words on galvanized steel, zinc fumes, and stick welding.
Galvanized steel is regular steel coated with zinc to make it rustproof. If you weld it without removing the coating, zinc creates the following problems:
- The arc quickly evaporates the zinc, resulting in a large plume of white fumes. Avoiding the fumes is the most important thing to do when welding galvanized steel.
- The arc also melts the zinc. Liquid zinc can penetrate the bead and the workpiece, making them brittle. If the weldment takes heavy stress, it may crack.
- Poor root penetration and lack of fusion are serious defects affecting the joint’s strength.
- The zinc vapors will destabilize the arc, resulting in excessive spatter.
- If zinc vapors remain in the weld metal, they will create porosity.
- The arc will be harder to start and maintain.
When the arc burns the zinc coating, it vaporizes, resulting in a large plume of fumes. Stick welding also generates a lot of welding fumes. As a result, the combined fumes can oversaturate a workshop in a short time, even if you use ventilation.
Inhaling this dense fume cloud will result in a temporary sickness called metal fume fever (pubmed.gov) and increase the risk for other long-term problems.
To avoid this, you should always work outside, position yourself to avoid the fumes, and wear a welding respirator.
To avoid the risk, read this article on how to remove the galvanized coating.
Except for the fume problem, stick welding can reduce the previous defects because:
- The stick rods are covered with flux material that contains many elements that clean the puddle and reduce porosity and spatter.
- Stick welding always creates a strong arc that burns the zinc at fast rates and penetrates the metal deeper.
- The strong gas coverage allows wide rod manipulation, so you can burn the zinc before it enters the puddle.
Stick welding is also very portable and can weld in windy environments, making it ideal since most galvanized steel is fabricated or repaired outdoors.
Now, let’s see the procedure step by step and what modifications you can make to minimize the defects.
1. Gather the equipment you need
The first step is to gather all the necessary welding personal protective equipment:
- A welding helmet is the most crucial PPE. It lets you see your work and protects your eyes and face from the arc’s radiation, sparks, spatter, and flying objects.
- Safety glasses protect the eyes from flying objects, including the slag material on the bead when you clean it. They also protect your eyes from UV rays if accidental arc strikes occur.
- If you use an angle grinder, wear earplugs or earmuffs.
- Thick welding gloves protect your hands from UV light, sparks, spatter, and hot metals.
- Fire-resistant clothes that cover all of your body. Never wear synthetic clothes.
- Leather boots. Grinding sparks and welding spatter can easily destroy synthetic shoes and burn your feet.
- A welding respirator with P100 filters. These filters can absorb almost every air pollutant when you weld galvanized steel. You can read this article on welding respirators for home welding to learn more about it.
You also want a chipping hammer and a wire brush to clean the slag covering, and the burned galvanization left on each bead.
Do a quick safety check to avoid surprises that may harm you or your work. For instance, don’t weld close to flammable materials or exposed electrical wires, set the correct helmet settings for outdoor or indoor welding, etc.
2. Clean the joint
Even if you don’t remove the coating, it would be best to remove any dirt around the joint. The zinc coating already makes welding difficult, and the presence of soil, dust, oil, etc., will make things worse. A wire brush and a rag can remove most of them.
3. Select the correct stick rod
The galvanized coating is very different from other coatings such as mill scale. One factor when choosing a rod is the silicon content because high silicon increases the risk of zinc cracking.
The best rods for most galvanized jobs are the E6010 and the E6011 because these rods:
- Create an aggressive arc that can burn the zinc.
- Have the lowest silicon content.
- Generate a lot of shielding gases, so you can use a wide rod manipulation to burn the coating.
- They can weld in all positions, including vertical-down.
The E6010 rods offer somewhat deeper penetration, but most low-cost welding machines cannot burn them. The only option left for most home or small workshop machines is the E6011.
Another restriction of E6010 rods is that they run only on DC+ polarity. The E6011 rods run on DC+ and AC.
The next best rods are the E7014 and the E6013 because they also have a low silicon content.
These are the easiest rods to use and great for home fabrications, but they don’t have the strong arc of the previous rods.
The E6013 is the rod you want to use if you stick weld thin metal, for example, less than 1/8″ (3.2 mm).
Finally, the popular E7018 is a heavy-duty rod. On clean metals, it creates weld metal that is superior in every way compared to the previous rods.
But it has a weakness against galvanized steel. It has almost two times more silicon than the previous rods. This greatly increases the risk of zinc cracking when you weld projects with demanding service conditions.
Because joint failure in heavy-duty projects can result in injuries and costly damages, it’s best to remove the galvanized coating and use E7018 rods only on clean metal.
However, if you weld simple projects, the E7018 can weld galvanized steel with minimal chances of zinc cracking.
When you select a rod, you can weld on similar scrap metal and do a manual bend test to test the joint’s strength.
You select the rod size considering the metal’s thickness and the joint type. As a general rule, you select a slightly thinner rod than the workpiece. If you have a large joint, for instance, a single-V or a double-V, the rod must be thin enough to reach the root. For example:
- If you have a square-butt joint and the workpiece is 1/8″ thick, you select a 3/32″ rod.
- If you have a single-V joint and the workpiece is 1/4″ thick, you select a 3/32″ rod for the root pass and a thicker 1/8″ rod for the next passes.
Weldpundit has detailed articles on the best welding rod for galvanized steel and how to select stick welding rods, including size and amperage.
4. Prepare the joint and clamp the workpieces
Preparing the joint of galvanized steel is similar to uncoated steel, with some modifications.
If you have a butt joint, you always leave a wider root gap than usual. This way, liquid or gaseous zinc can escape easier.
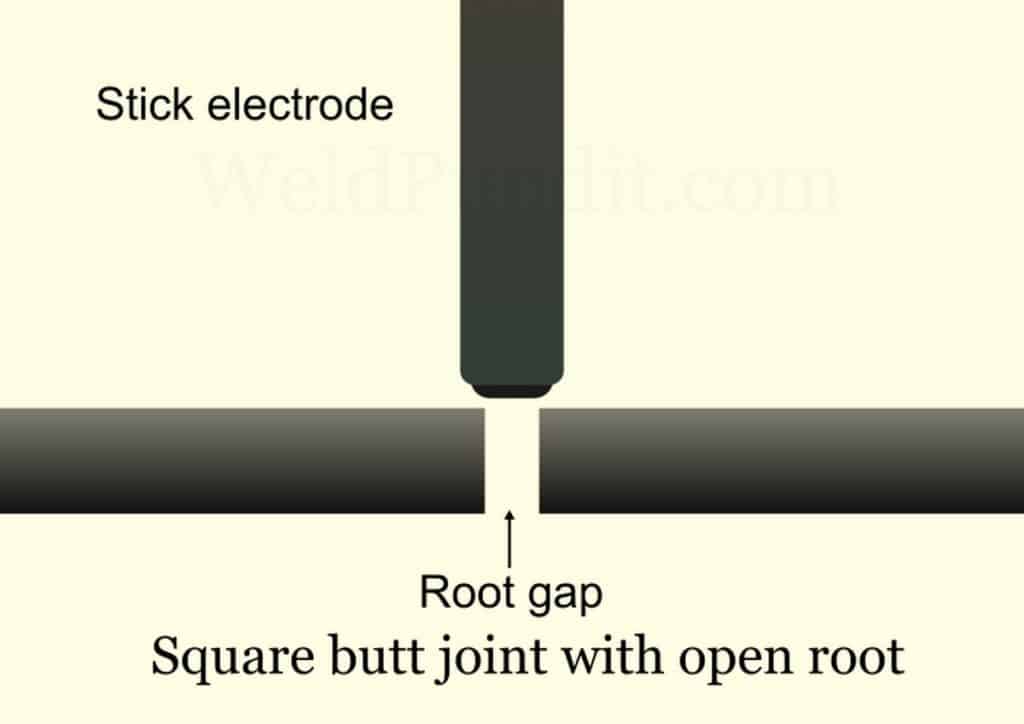
For the same reason, you want to avoid closed butt joints and always leave a small root opening.
If you weld from one side and the metals are thicker than 1/8″ (3.2 mm), bevel them at 30 degrees and make a single-V joint. Leave a wider root gap than usual.
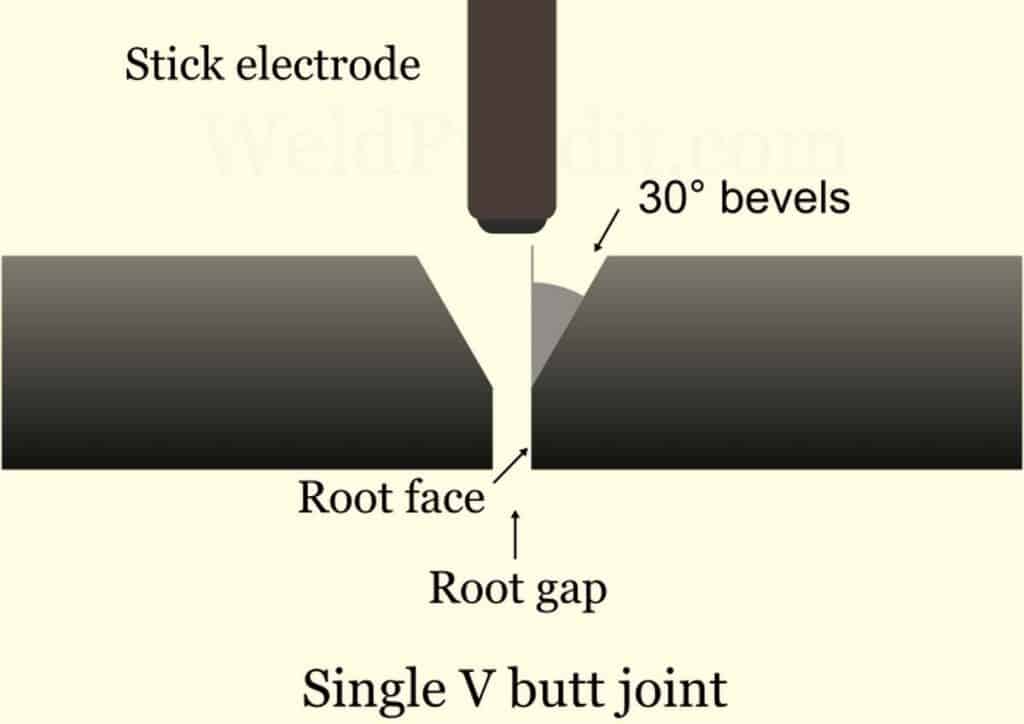
Fillet welds of tee and lap joints are the hardest to weld if you don’t remove the coating. That’s because fillet welds cover a larger part of the joint and burn more zinc. But even worse, these joints almost always don’t have root gaps.
As a result, the zinc fumes formed at the abutting surfaces cannot escape easily. Eventually, they will escape through the puddle when they gain enough pressure, creating excessive porosity. Liquid zinc will also contaminate the metals, increasing the cracking risk.
If the metals are thick, for example, more than 1/4″ (6.4 mm), you can leave a small 1/32-1/16″ (0.8-1.6 mm) gap. This way, the fumes can escape. You can use welding wires or rods to create this gap, then tack weld the joint and remove them.
Outside corner joints are the easiest because you don’t burn much of the galvanization.
Ensure you will always have a symmetrical fitup. Irregular joints may blow through at the wider or thinner parts. Furthermore, try to weld in the flat position if possible, since it’s the easiest one.
5. Set the correct amperage and tack the metals
Using a higher amperage (5%) to weld galvanized steel will help burn the zinc easier. It is more important if you weld fillet welds. Furthermore, the higher amperage will make the rod easier to start and prevent it from sticking to the metal.
For example, you have a 1/8″ E6011 rod, and you want to weld a horizontal fillet weld of a 3/16″ tee joint. Normally, you use 100A, but you set 105A or a bit higher for galvanized steel. Always run test beads on similar scrap metals to check the results.
Below is a chart with typical amperage ranges for the mentioned rods using DC+ polarity. For galvanized steel, you increase the amperage by 5%. If you use AC, increase by 10%.
Stick rod | 1/16″ 1.6mm | 5/64″ 2.0mm | 3/32″ 2.4mm | 1/8″ 3.2mm | 5/32″ 4.0mm | 3/16″ 4.8mm |
---|---|---|---|---|---|---|
E6010 &E6011 | – | – | 60-90 | 75-130 | 120-165 | 160-195 |
E6013 | 25-50 | 40-70 | 65-95 | 85-135 | 125-175 | 175-215 |
E7014 | – | – | 75-105 | 100-150 | 135-200 | 185-240 |
E7018 | – | – | 70-110 | 90-160 | 130-220 | 170-270 |
Each manufacturer recommends an amperage range for each rod they produce. Some ranges may be quite higher or lower than the previous chart. Always read the packaging before setting the amperage.
It would be best to use the DC+ polarity since it gives the hottest arc. The DC- is useful for sheet metals.
Use AC only when you experience the arc blow defect or your welder only supports this current type. The arc blow defect is a magnetic interference that points the arc away from the correct path.
Furthermore, if your welding machine has the hot-start and arc-force (or dig) functions, set them at high values. The hot-start helps to start the arc easier, and the arc-force prevents sticking the rod while welding.
Finally, tack weld the metals to keep them in place and avoid distortion. Tacking length depends on the thickness: the thicker the metals, the longer but larger the tacks.
6. Tips for stick welding galvanized steel
Now, let’s see some modifications and tips when you stick weld galvanized steel:
- The most significant change is to travel at a slower speed. Slow down by 90 or even 80%. This will input more heat into the workpiece and burn the zinc coating easier. One way to reduce the speed is to use wider rod manipulation. Try to avoid straight (or stringer) beads if possible because they use a fast traveling speed.
- When you want to burn coatings, you must use a pattern that keeps the arc in front of the puddle all the time. The whip and pause pattern is the best one, but not all rods can do that. In the following image, you can see the V pattern that’s also suitable. A circular pattern isn’t as effective because it doesn’t always point the arc in front of the puddle.
- The zinc coating interferes with the workpiece (or grounding) clamp connection. As a result, the current doesn’t flow correctly and the arc becomes more unstable. Try to connect the clamp as securely as possible.
- You should avoid striking the arc on the surface. Instead, start it in the joint or on the previous beads.
- Keep a short arc length, no more than the rod diameter. This will further reduce porosity, spatter, and slag inclusions. Also, a short arc length is very important when you weld in the vertical position because it will prevent liquid zinc from entering the puddle.
- Always fill the ending crater. If the crater is concave, the shrinkage forces may crack it, especially if there is zinc trapped inside it.
- Clean the slag covering before passing another bead to prevent slag inclusions.
- If you weld outdoors, and it’s cold, you will have serious problems. The arc will not start, and the rod will stick to the metal. If you manage to start the arc, it will feel like you weld with low amperage. To avoid this, preheat the joint with a flame torch up to 100 °F (38 °C).
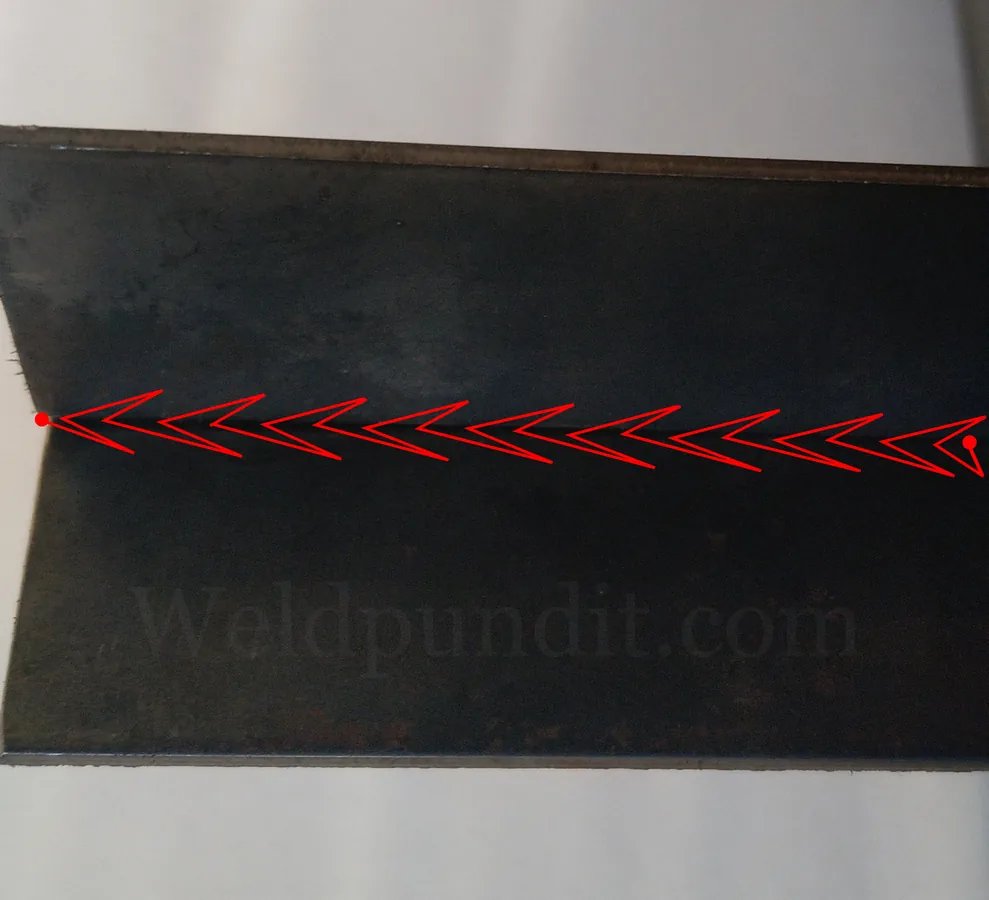
7. Restore the galvanization
When you finish welding, you must restore the metal’s corrosion resistance. That includes the new bead and the burned galvanization not only on the side you welded but all around the joint.
Furthermore, spatter and porosity left on the joint act as corrosion concentration points that you want to remove or cover.
The easiest way to fix this is to grind the joint with a 40-60 grit flap disc and wipe it with a clean cloth. After that, apply zinc-rich paint or spray on all exposed areas. We call this cold galvanization.
In a nutshell
When stick welding galvanized steel, the most important thing to do is avoid inhaling the fumes.
When you gather the tools and equipment, you want to select the correct rod, for most jobs an E6011.
If you weld a butt joint, you always leave a wider root gap. If you have a thick tee or lap joint, it would be best to leave a small gap between the metals to avoid trapped zinc.
Before you start welding, you set an amperage somewhat higher than normal.
It’s important to weld at a slower speed and use a pattern that always keeps the arc in front of the puddle.
Finally, you use zinc-rich paint to restore the galvanization after welding, especially if it’s exposed to a wet environment.
More Weldpundit articles
How to Stick Weld Stainless to Carbon Steel: Step by Step.
How to Stick Weld Cast Iron: With and Without Preheating.
How to Choose a Stick Welder: Best Entry-Level Characteristics.